What needs to be lubricated?
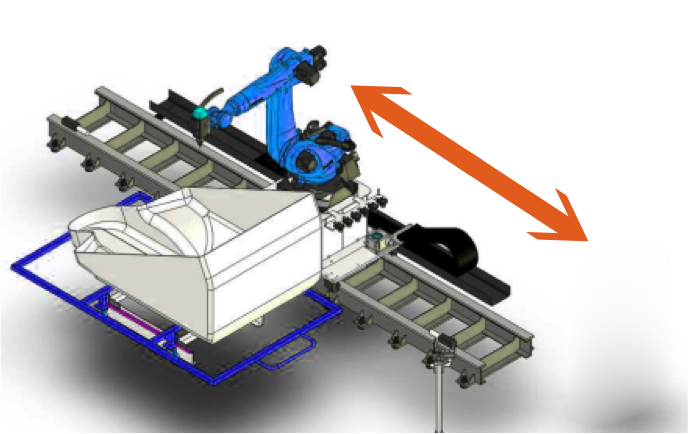
7th Axis for Robot Horizontal Motion
Manufacturing companies in every field have realized the best way to be competitive with price and quality is to automate their factories. This requirement to automate has created a large demand for 6 axis articulated arm robots. These robots perform many operations from material handling, painting and welding to actually machining parts. In order to expand the work envelope of the six-axis robot a linear seventh axis is added. This axis allows the robot to move horizontally from station to station or just provide access to larger parts being manufactured.
The seventh axis is typically driven by a rack and pinion system and supported by linear guides. In order to insure reliable operation and minimize downtime these components need to be properly lubricated. The best way to insure lubrication is with a multi-point automatic lubrication system.
Customized Solution
Redex, USA in conjunction with their partner DLS Schmieresystemes has developed complete systems for automatic lubrication of robot 7th axis. These systems are based on standard lubrication components that are adapted for easy installation on the 7th axis. Below is an example of one system.
Rack, Pinion & Linear Guide Lubrication System design
Installation 1
Installation 2
Multi-Point Lube System Components
The FlexxPUMP 400 lubricant delivery pump is the heart of the system.
FlexxPUMP 404DLS
The clear housing is the lubricant reservoir which can hold grease in cartridges or oil. The bottom metal housing holds the piston pump bodies. The piston pumps deliver the lubricant at a rate of 0.15 cc/stroke and pressure up to 1000 PSI. This means that the quantity and frequency of lubricating each point can be very accurately controlled. One FlexxPUMP 400 can provide two unique lubricant delivery rates. This is very well suited to lubricating a rack with one outlet and linear guides with a second outlet because linear guides require about 1/10th as much lubricant required by the rack and pinion.
There are actually two ways that the FlexxPUMP can be controlled. If there is a PLC on the seventh axis, each outlet can be activated with a 24V DC pulse of a specified duration. If a PLC is not available the pumps can be controlled in a time mode which specifies the time (in months) to complete one full cartridge of grease and the amount of pump strokes (or quantity of lubricant delivered) for each operating period. The pump can be powered by 24V DC or by battery for hard to access locations.
The FlexxPUMP also provides error signals for:
- Pressure exceeding 1000 PSI in case there is a clogged line
- Empty reservoir indicating it is time to replace the grease cartridge or refill with oil
- Electrical error (Low voltage or other electronic issues)
These allow for easy system monitoring.
In addition to the FlexxPUMP, a standard range of accessories is available to make sure the lubricant gets from the Pump to the element being lubricated. Examples of accessories are:
Accessories
![]() High Pressure Plastic Tubing | ![]() Open Cellular Polyurethane |
![]() Open Cellular Polyurethane Foam Roller for | ![]() Push-In Tube Connectors |
Splitters & Progressive Distributors
The FlexxPUMP and accessories are standard components which are normally in stock making for a cost effective industrial quality lubrication system that is readily available. Only the mounting brackets are designed and customized to the actual robot’s seventh axis.
Benefits
Incorporation of this automatic lubrication system on the seventh axis provides the following benefits:
- The correct amount of lubricant is applied to the lubrication point and eliminates the possibility of over lubrication or under lubrication when lubricant is applied manually.
- Correctly lubricated gears and bearings provide reliable operation and avoid downtime which can hold up production.
- The system provides the minimum amount of lubricant required to insure correct lubrication. This avoids housekeeping issues often associated with lubrication systems.
- Safety by avoiding the need for maintenance technicians to enter the potentially hazardous moving zone of the robot.
Get Expert Advise
Each member of the Redex sales and engineering team is available to provide the technical expertise, service and support to meet customers’ application requirements. Please feel free to contact us with your 7th axis lubrication requirements.